Understanding Pipe Corrosion
Corrosion in sprinkler piping is a major cause of sprinkler system failures. According to the National Fire Protection Association (NFPA), 10% of sprinkler system failures are caused by corrosion.
Corrosion is caused by the combination of metal piping, moisture, and air and ultimately, results in reduced water flow, pinhole leaks and sprinkler head or piping blockage.
Right now, water is sitting in the pipes of every commercial building with a functioning fire suppression system. This is great to know in case there is a fire in the building, but while there is not a fire, that water is just sitting there.
These fire system pipes are made of metal and the water is the main catalyst for rust and mineral build up.
Overtime, the water in the pipes begin to eat away at your pipes, causing corrosion, and threatening the viability and integrity of the system.
Metro-Phoenix Hard Water Levels
Here in Arizona, hard water ( a common term for water with high concentrations of calcium and magnesium bicarbonates) translates to fire system piping issues. The minerals in the water build up in pipes, which then calcify and corrode the pipes that carry the water to the sprinklers.
You’ve likely seen the results of hard water on a faucet. The white build-up you see at the end of the faucet is the result of hard water- resembling mineral growth. That same build-up occurs in your fire sprinkler piping system.
The Phoenix-Metro area has a hard water problem, due to its soils and water source.
For reference, water with more than 3.5 grains of calcium and magnesium bicarbonates per gallon is deemed “hard water. In the Valley, Gilbert has the lowest levels at 9 grains per gallon.
The annual/ average hard water levels of other cities include:
- Chandler: 16.5
- Glendale: 17.5
- Goodyear: 24
- Mesa: 17
- Peoria: 10.5
- Phoenix: 14.9
- Tempe: 13.9
If you work, live, or manage a building in the Phoenix Metropolitan area, you should have your building’s water pipes inspected for corrosion, blockages, and leakages.
How Often Should My Fire Sprinkler System be Inspected?
The National Fire Protection Association (NFPA) requires certain fire suppression equipment to undergo inspection. Inspections are weekly, monthly, quarterly, semiannually, annually, or at five-year intervals, based on the type of system. Requirements mandate building owners keep records of fire sprinkler system inspection, maintenance, and testing.
To maintain compliance and streamline the process, work with a qualified fire sprinkler system inspection company. This ensures your system is inspected and maintained according to the requirements laid out by national and local codes, as well as for the building’s occupancy type and system components.
The NFPA recommends sprinkler system inspections according to the following schedule:
Every week or month:
- For dry or wet pipe, pre-action, and deluge systems, gauges and control valve inspections
Quarterly:
- Alarms, hydraulic nameplate, and fire department connection inspections
- Alarms and main drain testing
Annually:
- Hanger and seismic bracing, spare sprinklers, sprinklers, pipe and fitting, and signage inspections
- Main drain, fire pump, water flow, alarm devices, deluge, antifreeze solution, and pre-action valve testing
- For dry pipe systems, valve and low point drain maintenance
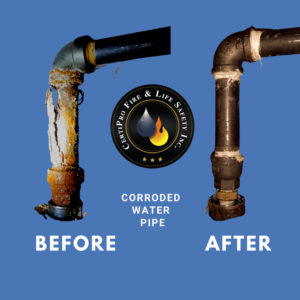